Quels aciers pour les voitures de demain avec ArcelorMittal et l'UTC ?
Le centre de recherches Global R&D Montataire d’ArcelorMittal et l’Université de technologie de Compiègne ont présenté les avancées de leur laboratoire commun FuseMetal, créé il y a quatre ans, dans les domaines des aciers dits de « 3e génération ». Objectif : alléger les véhicules automobiles, réduire les quantités d’acier utilisé et les émissions de gaz à effet de serre.

Le
laboratoire commun FuseMetal est né de la volonté conjointe
d’acteurs du laboratoire Roberval de l’UTC et du centre de
recherches Global R&D Montataire d’ArcelorMittal d’unir leurs
forces afin d’aborder des thématiques de recherche technologique
liées à l’allègement des structures et à l’emploi optimum des
matériaux.
À la base, ce laboratoire FuseMetal a été créé en avril 2019, dans le cadre d’un appel à projet « Équipe mixte de recherche » lancé par la région Hauts-de-France. Quatre ans après sa création, il présentait, mardi 23 mai, les résultats de ses recherches dans les domaines des aciers dits de « 3eme génération » et de la fabrication additive dont le but est d'alléger les véhicules automobiles, réduire les quantités d’acier utilisé et ainsi les émissions de gaz à effet de serre. Matériau de référence de l’industrie automobile - loin devant les alliages d’aluminium, les plastiques ou les verres - l’acier est au cœur des stratégies visant à réduire les émissions de CO2 du secteur de la mobilité. Dans son innovation, les activités du laboratoire commun FuseMetal s’articulent autour du soudage des aciers de très haute résistance de troisième génération et de la fabrication additive des pièces en acier.
Développer des solutions d’allégement des véhicules
« Les aciers de haute résistance sont bien connus des constructeurs et représentent près de 60% des aciers utilisés dans le secteur automobile. Les générations les plus récentes de ces aciers offrent des niveaux de résistance (jusqu’à 1800 MPa de résistance mécanique) et des capacités de mise en forme améliorées qui permettent des allégements supplémentaires de l’ordre de 20%. Ces aciers de très haute résistance peuvent être utilisés sous la forme de flans raboutés par soudage laser, ce qui permet d’ajuster l’épaisseur et le grade d’acier au besoin fonctionnel et aussi de réduire la quantité de matériaux utilisés en réduisant les chutes. On a donc un double gain, un allégement de la structure des véhicules qui conduit à une consommation en énergie réduite et une moindre consommation de matériaux, les deux concourant à une diminution des émissions de gaz à effet de serre », explique Francis Schmit, chef de programme R&D au sein du groupe ArcelorMittal et directeur adjoint de FuseMetal qui compte actuellement 35 membres dont 70% de chercheurs et personnel d’appui technique de l’UTC et 30% de chercheurs et techniciens d’ArcelorMittal, ainsi que six doctorants et deux ingénieurs de recherche. Il est également soutenu par le Fonds européen de développement régional opéré par la Région Hauts-de-France.
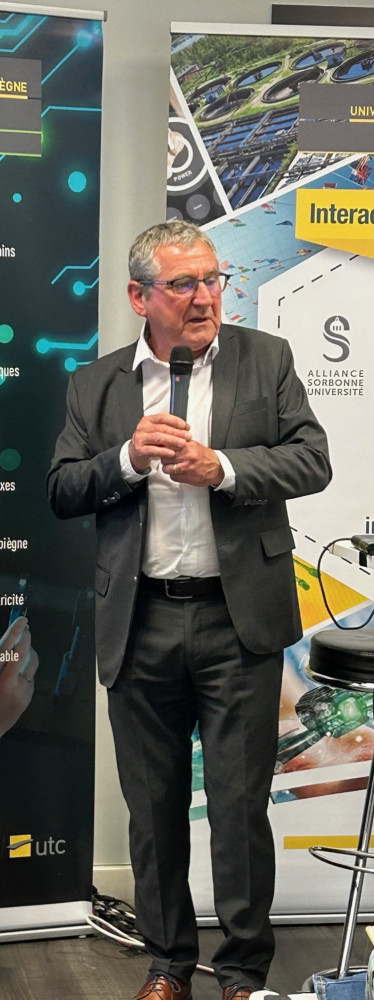
Vers une filière acier décarbonée
Les
aciers de très haute résistance de troisième génération se
caractérisent par des compositions chimiques et des microstructures
très élaborées qui complexifient leur soudabilité. « Ces
difficultés ne peuvent pas être contournées de manière empirique
par une simple adaptation des paramètres de soudage, mais
nécessitent la mise en place de démarches scientifiques prenant en
compte l’ensemble des phénomènes physiques intervenant lors du
soudage de ces aciers
», précise Marion Risbet, professeure à l’UTC et directrice de
FuseMetal. L’objectif
de cette thématique est donc de déterminer des conditions
d’assemblage optimales des aciers hautes performances en
établissant les relations entre les paramètres du procédé, la
microstructure de la soudure et sa tenue mécanique avec une approche
couplée associant des travaux expérimentaux, la modélisation
physique et la simulation numérique. »
Concernant la fabrication additive des pièces en acier, un des objectifs poursuivis est la modélisation multi-physique du procédé de fabrication additive. L’autre objectif concerne la fabrication additive d’outils de mise en forme destinés à l’emboutissage à chaud. « Au-delà d’avancés techniques, importantes pour ArcelorMittal et ses clients, le laboratoire FuseMetal permet au groupe d’établir un lien fort avec une université de premier plan, avec tous les avantages que l’on peut imaginer en termes de développement des compétences et de recrutement. C’est un partenariat gagnant-gagnant pour les deux entités », conclut Francis Schmit.
Le contrat liant ArcelorMittal et le laboratoire Roberval sera poursuivi avec des objectifs techniques redéfinis prenant en compte les enjeux liés aux évolutions technologiques dans le secteur automobile et la mise en place de filières de fabrication décarbonée des aciers à l'horizon 2050.
À lire aussi : ArcelorMittal : une nouvelle unité de production d’acier électrique